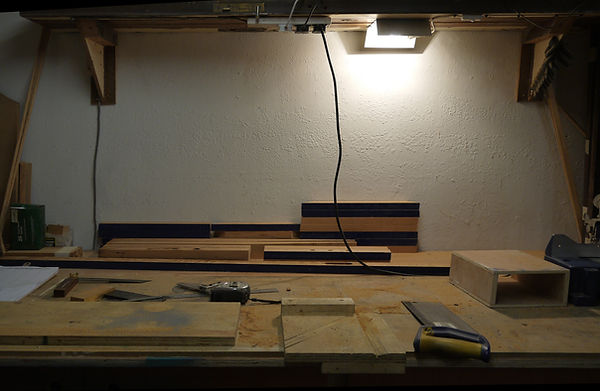
Batch production Door chairs
Hand cut components
In order to minimise wastage, components are grouped by angle and marked out along the processed timber in advance so that a single cut provides two matching angles (component ends).
These are roughed out by hand before being accurately trimmed to size.
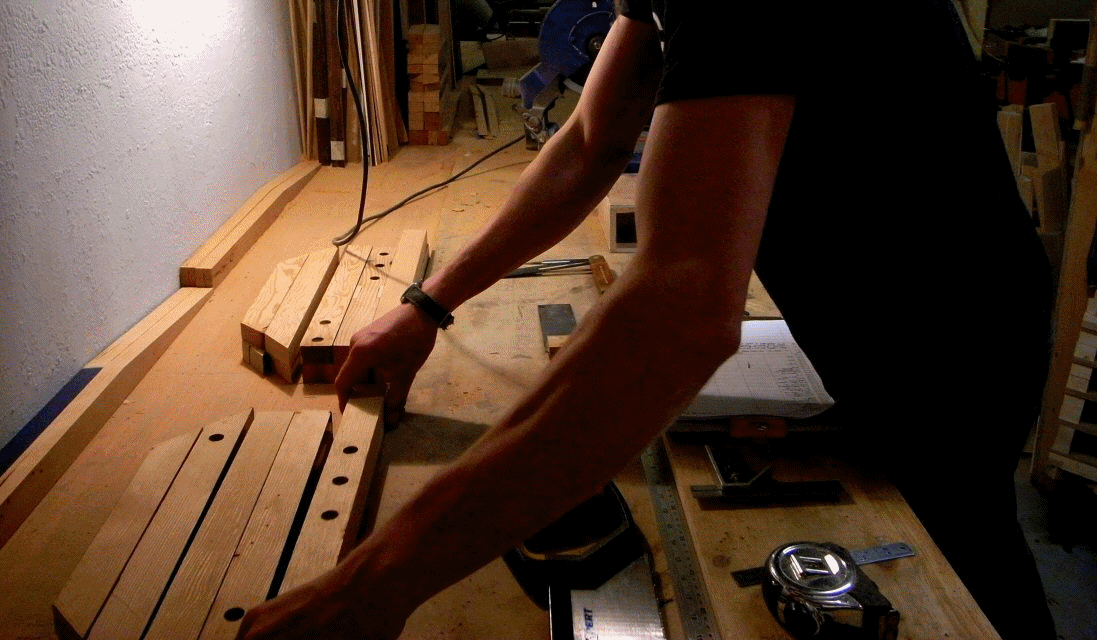
Halving joints (lap joints) -cutting
As a relatively simple yet effective joinery technique, halving (or lap) joints are cut into the components, and the faces cleaned up ready for joining.
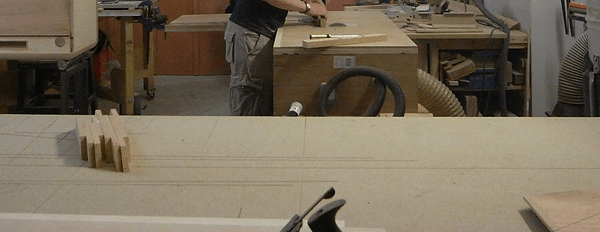
Joining the profiles
To optimise the joining process, a joining frame is used to simultaneously press 12 joints with a single sash clamp.
Each profile is glued, assembled and then mounted in the frame between pressing plates.
One long clamp passes through the 4 profiles, 8 dividing plates and two endplates to distribute localised pressure at 3 points on each profile.
A further two clamps press a bar against the mounted profiles to form the correct angle.


Seats and backs
With the frames nearly ready, the back rests and seats are pressed, trimmed and rebated for the final assembly.
In keeping with preservation and batch processing, the seat design makes use of an historic joinery detail from its previous incarnation as a door.
Acting like an engineered tongue and groove joint, this detail allows the tops to be pressed into form while the glue is going off.
A vertical press system is used to form 2 backrests and 2 seats simultaneously.
Sash clamps are used to press each layer in sequence as retaining wedges hold the layer previous in place.
Lengths of timber secure the fully loaded press.


Assembling the frames
After another clean-up and some further joinery, the paired profiles are assembled into frames to create the final structure.
